Politics
Confronting the Supply Chain Crisis
A pandemic-driven shortage of parts and labor has combined with a congested transport system to create an inflationary spike, with shipping rates doubling on some routes.
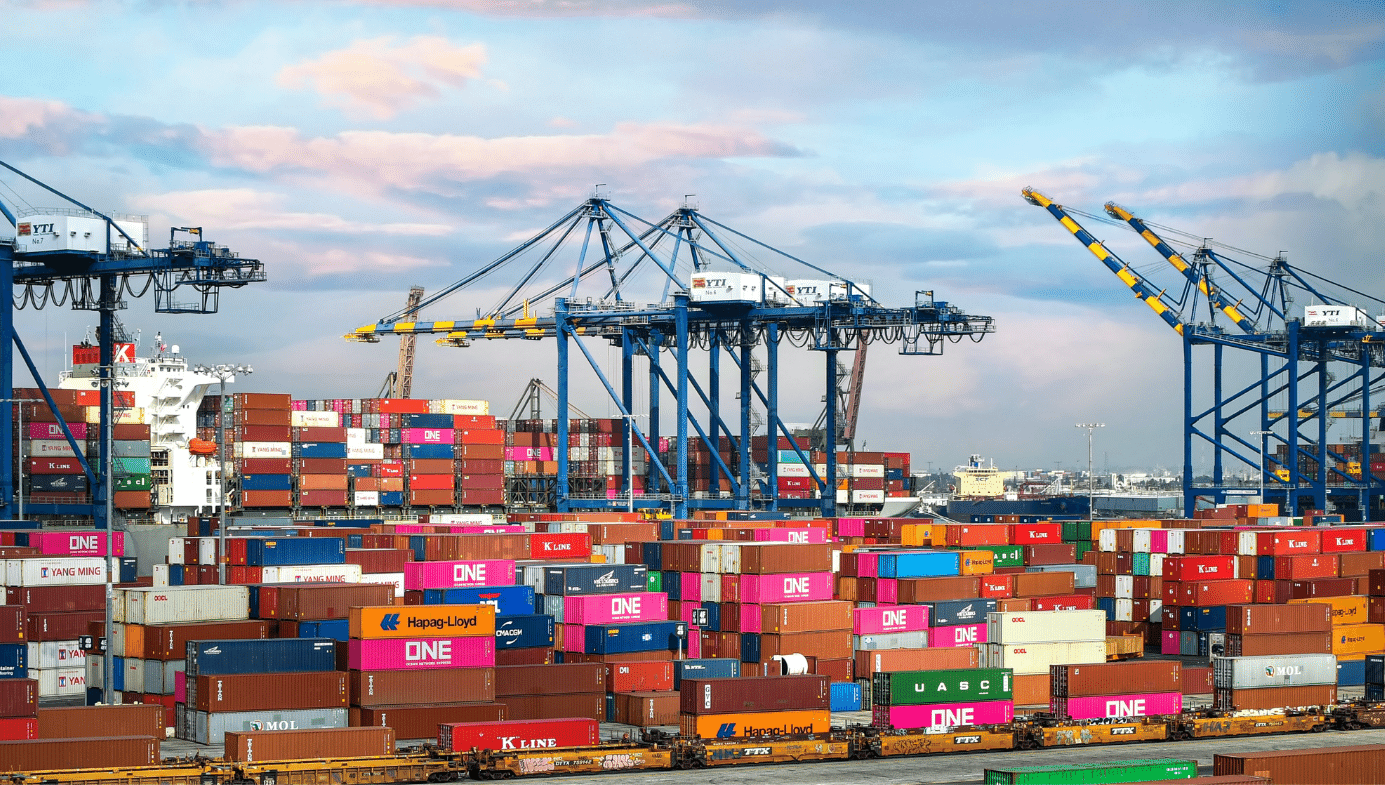
For a generation, the Long Beach and Los Angeles harbors in California handled more than 40 percent of all container cargo headed into the US and epitomized the power of a globalizing economy. Today, the ships—mostly from Asia—still dock, but they must wait in a seemingly endless conga line of as many as 60 vessels, sometimes for as long as three weeks. These are the worst delays in modern history, and the price per container has risen to as much as 10 times its cost before the pandemic. The shipping crisis is now projected to last through 2023.
A pandemic-driven shortage of parts and labor has combined with a congested transport system to create an inflationary spike, with shipping rates doubling on some routes. Prices for everything from soybeans to natural gas have soared as supplies take longer to produce and arrive, and this high inflation is wiping out wage gains in the US, the UK, and Germany. The chaos on the ground may not disturb the lifestyles of the tech and financial elites, but it is hurting the middle and working classes, the groups most threatened by surging inflation.
The supply chain disaster has also revealed the existence of crippling economic dependence, particularly on China, in high-income countries. Today, whole industries in the West—from medical equipment to chip and car makers to food—rely on China for finished products and key components. When China cannot (or decides not to) supply these parts, whole industries suffer debilitating supply chain shortages. The notion of a rational, self-regulating market system is unraveling and may yet presage the demise of the prevailing neoliberal era.
Walking away from production
For generations, business consultants have persuaded businesses large and small to move their production to China in search of cheaper costs. This has had a devastating effect, particularly in the United States, where between 2004 and 2017, the share of world manufacturing shrank from 15 to 10 percent while reliance on Chinese inputs doubled. The trade deficit with China, according to the Economic Policy Institute, has cost as many as 3.7 million jobs since 2000. The consequences have also been severe in the UK, which suffered 1.5 million job losses in manufacturing between 1997 and 2009, in part due to climate policies that threaten the last vestiges of heavy industry in the country that invented it.
In the face of these trends, the general response of the Western elites has been “Why worry?” Reflecting the ideological leanings of the American establishment, Christina D. Romer, the former head of the Council of Economic Advisers in the Obama administration, dismissed concerns about manufacturing policy as nostalgic “sentiment,” declaring, “American consumers value health care and haircuts as much as washing machines and hair dryers.”
But unlike the local hair salon, the market for washing machines is national and global and these goods have to be transported, often over great distances. A factory that makes parts for washing machines in a city, state, or region draws money to the local community. Moreover, manufacturing has one of the highest multiplier effects of any sector—one manufacturing job in a community is likely to generate numerous other direct, indirect, and induced jobs, both locally and elsewhere.
Pandemic lessons
In the midst of the pandemic, even the world’s richest regions—the European Union, the United Kingdom, North America—found themselves without basic medical equipment like masks, and even the compounds needed to make critical chemical treatments. In the early critical months, “China's decision to block exports of these goods led to widespread shortages,” observes Richard Haass, President of the Council on Foreign Relations. “There is also the concern that an increasingly assertive China might seek to exploit the world's dependence on it for political purposes.”
This disaster, now playing out across the industrial landscape, reflects the fracturing of supply chains over several decades. A generation of politicians, economists, and pundits, particularly in Anglo-Saxon countries like Australia, have paid little attention to nurturing the “industrial commons,” which encompass production, research and development, supply chains, embedded process development, and engineering capacity.
This pattern affects industries besides medical equipment. This year, auto production was curtailed due to a worldwide shortage of semiconductors tied to a recent drought in Taiwan. America’s push into renewables threatens to further bolster China’s dominance of the solar panel industry and production of the essential metals needed to produce “clean” energy and electric cars. The West’s trade deficit now extends even to high-tech products. When companies move production abroad, they often shift research and development as well. Remarkably, this has also included sources of critical components for military goods, many of which are now produced in China.
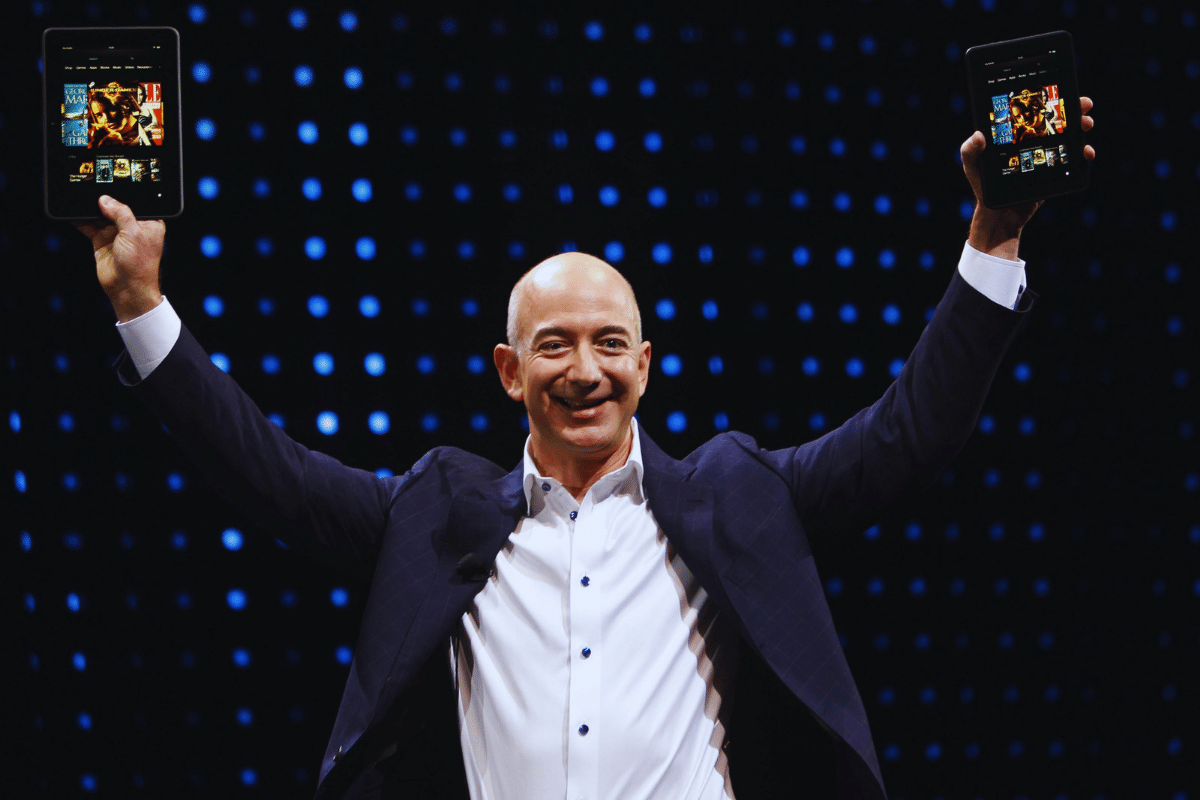
Reshoring: A possible answer
Camille Farhat—a former top executive at General Electric, Baxter, and Medtronic, and now CEO of Michigan-based manufacturer RTI Surgical—told me that many products, including medical supplies, can be produced domestically. Farhat hopes the pandemic will convince other business leaders to stop “destroying the supply ecosystem” that makes production possible. “To stay safe, you have to do contingency planning—you have to restore the network and maintain surplus production capacity. Hopefully, we are learning that lesson.” There are signs that some are heeding Farhat’s advice. Japan, France, the UK, and the European Union all recognize that dependence on China carries enormous political and economic risks. Japan is even offering loans to lure companies back home from China.
There are signs of some change in the corporate suite as well, even predating the current crisis. McKinsey and Company surveyed supply chain executives last year and found that nearly all respondents believe their supply chains are too vulnerable. According to March 2020’s Thomas Industrial Survey, COVID-19 supply chain disruptions aggravated an appetite for locally sourced materials and services—up to 70 percent of firms surveyed said they were “likely” or “extremely likely” to re-shore in the coming years. Similarly, a UBS study revealed that as many as 50 or 60 percent of firms now producing in China have moved or are planning to move.
This shift includes some major companies, like Black and Decker, who have moved production to a new facility in Fort Worth, Texas, as part of its reshoring strategy. Appliance giant Whirlpool reshored 400 jobs, along with General Electric, Apple, Caterpillar, Goodyear, General Motors, and Polaris. Little Tikes, a major American toy maker, has started shifting production out of China and back to Ohio. When Little Tikes started out more than 40 years ago, everything was made in the United States, but most production moved to China in the 1980s and ‘90s, when the Chinese manufacturing sector began to take off. Now, “the wheel is kind of coming full circle,” Executive vice president and worldwide general manager Thomas Richmond told me.
Of course, such moves will be resisted by companies that have grown hopelessly dependent on far-flung supply chains and no longer possess the skills to make their own products. Some analysts suggest that large-scale reshoring to North America will require strong government action. Yet there are reasons for optimism. President Trump's tariffs may not have done much to revive US manufacturing, but the Reshoring Initiative’s Harry Moser told me that the annual number of jobs returning from offshore has increased from 6,000 in 2010 to over 400,000 in 2019. Cumulative jobs brought back represent about five percent of the United States’ total industrial employment. In 2019, for the first time in a decade, the percentage of manufacturing goods imported to the US dropped, notes a recent Kearny study, with much of the shift coming from east Asia.
The China challenge
The supply chain crisis has made plain the grave threat posed by China’s rise. In the early stages of China's embrace of capitalism, the country’s industrial push was widely welcomed as a triumph of liberal globalization. China, it was believed, simply wanted to succeed, and would do so in a manner at least somewhat congruent with Western values. Its trajectory was expected to follow that of Japan, Singapore, or South Korea, all of which lack China’s military power, both in population and resources.
But under the leadership of Xi Jinping, China has nurtured an economy that works in a profoundly different way to those of capitalist countries. In the West, profits and individual wealth accumulation drive economic progress. Although Chinese people may also want to get rich, the primary goal of the CCP is to bolster the Middle Kingdom’s global power and influence. In China, the regime employs its power to restrain and even imprison the country’s entrepreneurs if they defy its authority. Social media is used as a political tool to promote China’s ascendency, even on ostensibly frivolous sites like Tik Tok.
China’s agenda has stretched beyond consolidating its hold on existing industries. Now it seeks to dominate such fields as artificial intelligence, bio-medicine, and the dominance of space that will likely shape the future economy. Economist Yi-Zheng Lian argues that stealing technology is now encouraged as China becomes a “nation of patriotic thieves.” The basic rules that underpin capitalist economies simply do not much matter, big time investors now lament.
China is also determined to promote its alternative authoritarian model of governance, particularly in developing countries. This drive could accelerate with China’s military expansion, and may yet include the conquest of Taiwan, which is now the world’s leader in semiconductor technology. The feisty island nation is now subject to aerial incursions from the mainland and could be blockaded. The Taiwan Semiconductor Manufacturing Company’s decision to build a $12 billion new plant in Arizona could be critical to assuring secure supplies for America’s manufacturers.
Needed: A policy and political response
Revitalizing our “industrial commons” requires bold new initiatives and measures from our economic past, which saw some very successful efforts to spark industrial growth during World War Two and the Cold War. Indeed, as two Harvard researchers have suggested, “Believing in the power of markets does not preclude the judicious use of appropriate government policies.”
While rejecting Trump’s crude unilateral approach, the Biden administration has continued to pursue many of its predecessor’s themes, including proposals to boost the domestic semiconductor and steel industries. The Biden plan would spend $300 billion on R&D to revitalize American industrial competitiveness and invest in alternatives to four-year colleges, trade schools, apprenticeships, and community colleges. A more ambitious part of the plan involves the use of taxes, subsidies, and public-private partnerships to encourage companies to retain the capacity to make critical supplies during a national emergency.
Reshoring will require tariffs and bans, but also incentives, including tax policies that encourage industrial investments, loans and loan guarantees, grants, public-private partnerships, and supportive educational and physical infrastructure. Additionally, steps could be taken to promote the development of critical rare metals outside of China.
Western countries could also justify shifts away from China on environmental grounds. For businesses and consumers, attempts to move out of China could cost as much as $1 trillion, but would detach firms from the country’s notoriously high carbon supply chains, which emit more greenhouse gasses than the United States and the European Union combined. Indeed, according to one recent study, China is home to 23 of the 25 largest cities in terms of GHG emissions.
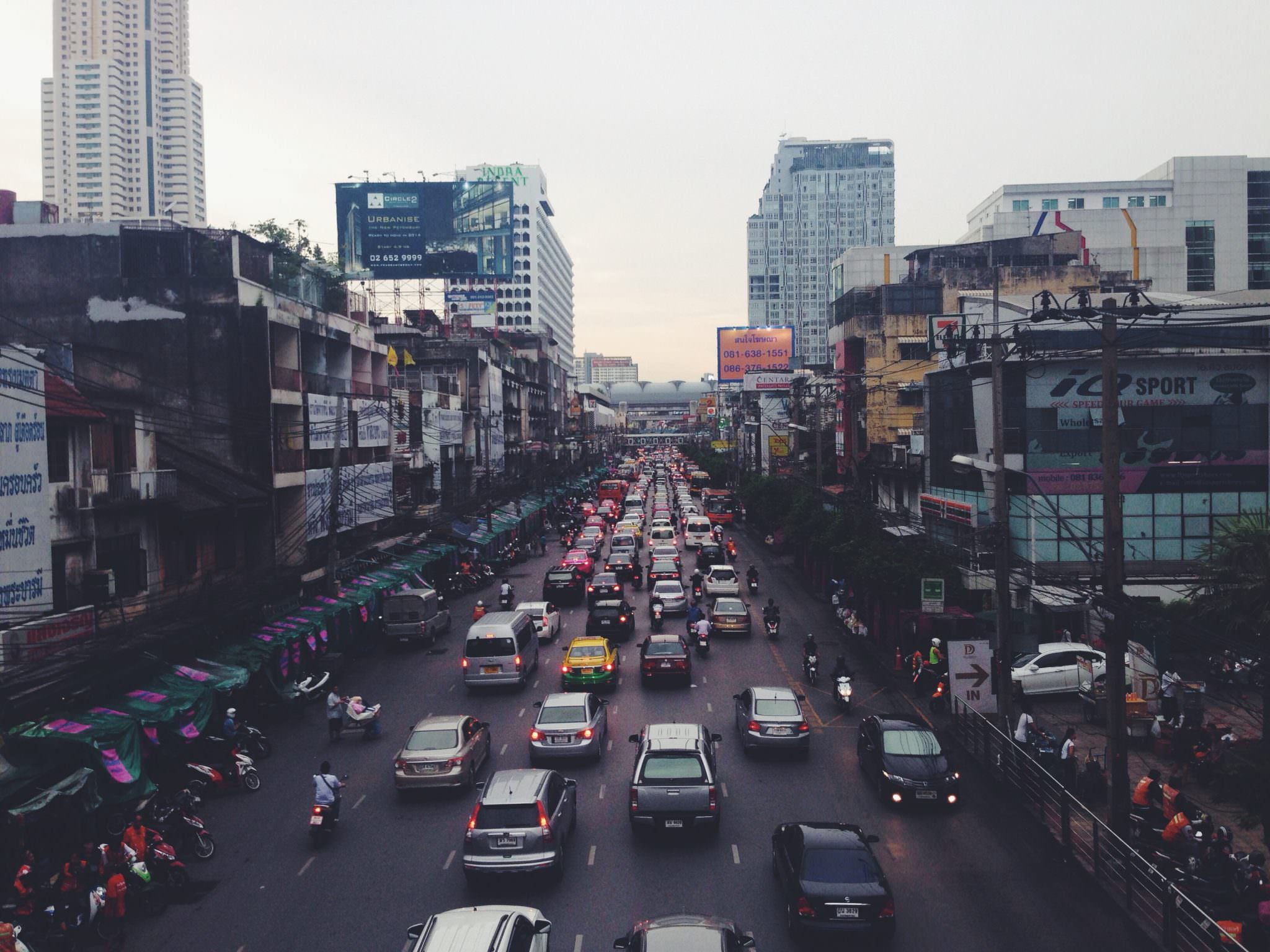
A post-globalist politics?
Addressing our supply chain vulnerabilities is not just good policy but also good politics. Robust efforts to counter China’s mounting challenge in science and technology, such as the US Innovation and Competitiveness Act, passed the Senate by a wide margin. A recent survey by the left-leaning Center for American Progress found that far more Americans prioritize protecting US jobs and reducing illegal immigration than progressive goals like combatting climate change and improving relations with allies.
New public opinion poll. Insights into what Americans want US foreign policy objectives to be. Promoting democracy and freedoms comes in dead last. pic.twitter.com/RnD7GdLOYm
— Bonnie Glaser / 葛來儀 🇺🇦 (@BonnieGlaser) June 3, 2021
Despite the much-ballyhooed consumer benefits of low-cost imports, the vast majority of Americans seem to be willing to pay higher prices that would come from moving production out of China—a fact that has encouraged retailers such as Walmart to seek out more domestic suppliers. The current supply chain crisis can only reinforce these trends. Economic boycotts of Chinese goods and firms—a successful example of which is the US attempt to thwart telecommunications giant Huawei—may be a harbinger of things to come, at least in strategically critical areas.
Some may see such an effort as doomed, particularly on Wall Street, a bastion of pro-China sentiment. But the Middle Kingdom may be far more vulnerable than widely thought. China’s financial system is only now feeling the impact of massive but unwise investments in high-rise offices and residential towers, epitomized by the Evergrande’s pending bankruptcy. A rapid decline in the workforce by over 200 million by 2050, a stubbornly low birth rate, and growing class conflict could also pose challenges and provide opportunities for competitors. More critically, Chinese regime controls could derail innovation. Certainly, blocking data and analysis from the rest of the world is not the route to information-era dominance.
Handing the industrial and technological future to authoritarian states is a recipe for undermining our own democracy. Of course, free countries will still trade with autocracies, which seem to be ascendant. But the focus needs to be on maintaining primary supply chains with partners who essentially conform to the rule of law and are not seeking to establish a global hegemony. What’s needed is a series of alliances with likeminded countries that generally follow liberal capitalist values and legal norms. This can be seen in the new defense pact between the US, the UK, and Australia, with potential growing ties to Japan, South Korea, and India.
In the long run, capitalist order can only be maintained by a common belief in basic principles of fairness and legality. The ships stalled at sea and empty supermarket shelves and relentlessly higher prices represent warning signs of a new and dangerous economic reality. We can either accept dependency as “the new normal” or we can address it directly, abandoning dreams in favor of approaches based on reality and greater self-reliance.